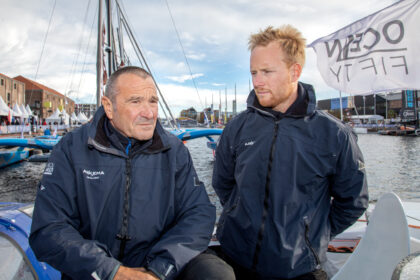
Arkema 4 a franchi la ligne d’arrivée de la 15ème édition de la Transat Jacques Vabre en septième position de la catégorie Ocean Fifty. Le duo Quentin Vlamynck – Lalou Roucayrol termine à une journée du vainqueur mais l’important n’est pas là.
Lalou Roucayrol a construit son nouveau trimaran avec un objectif de recyclabilité élevé, basé sur l’usage de la résine thermoplastique Elium® de son partenaire historique, la société Arkema premier chimiste français, ancienne filiale de Total.
Avec cette Transat aboutie, Lalou valide donc le concept qu’il avait présenté à Bruits de Ponton avant son départ du Havre.
Bruits de Ponton : « Pourquoi vos bateaux ne sont-ils pas recyclables ? Quelle est la problématique du composite ? »
Lalou Roucayrol : « Nos bateaux utilisent du composite réalisé avec du tissu mélangé avec de la résine dont la polymérisation donne une forme dure. Le tissu est orienté en fonction de la charge et des efforts. Les résines thermodurcissables utilisées sont difficiles à recycle, en effet il n’est pas possible de séparer les fibres de la résine autrement que par bain chimique, non recyclable. Il faut savoir que les pales d’éoliennes représentent la plus grande part de composites produits dans le monde, elles ne sont pas recyclées et finissent dans d’immenses sanctuaires.
La résine thermoplastique Elium® est conçue pour des bateaux composites recyclables. Elle est proche mécaniquement d’une résine époxy, et même supérieure aux résines polyesters qui ont été abandonnées pour les bateaux de course mais que l’on retrouve dans les bateaux de plaisance. Des épaisseurs peuvent ensuite être rajoutées pour gagner de l’inertie et du poids sur la pièce : le sandwich peut être en nid d’abeille mais pour notre classe Ocean Fifty, l’usage de la mousse est obligatoire.
©Matthew BENDER © Alexis Cheziere © Vincent Olivaud
Il existe deux options : la mousse PVC dont la fabrication consomme énormément d’énergie et dont la recyclabilité est problématique quand le PVC est mélangé. L’alternative est la mousse PET issue typiquement du recyclage de bouteilles d’eau en plastique.
Nous avons donc utilisé des mousse PET avec la résine Elium® sur une fibre de verre avec un composant totalement compatible en recyclabilité. »
Bruits de Ponton : Quels sont les objectifs de cet Ocean Fifty pilote ? Quel est l’impact sur la performance de la recherche de recyclabilité ?
Lalou Roucayrol: «Ce pilote Arkema vise à démontrer la réalité de la recyclabilité. Le moule des pièces composites a été fabriqué avec notre résine, ensuite nous avons tronçonné notre moule thermoplastique en plaques d’un mètre, broyé en copeaux partis au recyclage chez Arkema avec un four à pyrolyse basse température autour de 400°.
Nous avons ainsi séparé la fibre de la résine, récupéré cette dernière à 95% pour fabriquer le carénage du bras avant. Pour cette pièce il s’agit vraiment d’une approche circulaire : dès la conception, l’usage post recyclage était identifié. Nous avons néanmoins dû garder une approche traditionnelle car nous avançons en même temps que la technologie.
Nous travaillons avec Elium® depuis 2014, au début la résine fonctionnait mal au contact, elle a su évoluer avec des versions successives. Notre Mini avait été fait avec une mousse PVC faute de mousse PET disponible. Ensuite pour le niveau de performance voulu pour le trimaran, nous avons dû faire de la construction classique en pré-imprégné c’est-à-dire avec la résine déjà dans le tissu pour les bras de liaison, la coque et les flotteurs.
recyclage – ©Maxence Peyras
Néanmoins les partie rapportées, carénages, partie de pont visible au-dessus du pont structurel nous permettent d’atteindre un taux de recyclabilité de 20%. La mousse PET est vraiment le point clé, issue du recyclage et recyclable à nouveau. Notre prochain Class40 qui sera bientôt mis à l’eau sera lui 100% recyclable. Nous avions sacrifié de la performance sur le Mini, c’était une première, avec des marges importantes de sécurité.
Sur le multi, il n’y pas de prise pris de poids liée au matériau de recyclage et nous sommes confiant dans les capacités de vitesse du bateau. Enfin le Class40 est le sistership de Crosscall et nous produisons des pièces brutes dans les mêmes poids. »
Bruits de ponton : Pourquoi cette démarche ? quel est le sens pour toi ?
Lalou Roucayrol : « Il faut bien comprendre que jusqu’à présent, les anciennes pièces étaient broyées ou enfouies, même si les bateaux de course seront remployés, leur fin de vie est compliquée. Au mieux les déchets valorisables thermiquement peuvent partir en incinération mais cela encrasse les filtres assez rapidement, certains cimentiers utilisent le broyat en carburant et des essais d’amalgame autoroutier ont été testés.
Il n’y a pas de valeur ajoutée sur le composite, le déconstruire coute cher, il n’y a donc pas de marché. L’objectif consiste vraiment à récupérer la résine, la fibre et la mousse. Après il restera un gros travail sur les voiles qui servent dans le meilleur des cas à faire des sacs. Je trouve le lin intéressant, la fibre de basalte également mais le problème vient du liant utilisé qui rend le produit final non recyclable.
Néanmoins la production d’un produit biosourcé est sur un cycle plus court car le lin vient du champ d’à côté et cela permet de descendre le bilan carbone. Nous ne sommes pas dans le nouveau monde, les avions volent, les cargos tournent, faire des bateaux de compétitions recyclables permet la prise de conscience afin de limiter une production effrénée et infinie.
Nous ne changerons pas le monde dans les dix années qui viennent car c’est l’économie qui nous gère. Les solutions pour sortir des modèles économiques lourds viendront des entreprises, des utilisateurs qui accepteront de payer plus cher du circuit court.
Notre démarche est une microgoutte d’eau mais j’ai l’impression que nous ferons un fleuve à terme. »
[…] limité par les règlements de la Class40 alors qu’un Imoca en embarque des kilos et des kilos (A ce sujet, Lalou Roucayrol nous avait partagé sa démarche) . Nous sommes donc très fiers d’avoir construit cette course, le standard sera très élevé. […]